Long Live the Capsule! – unique Entry Engineering project
This project bears quite a complex name: “Research and development of a multifunctional automated filling device with production software and single-use capsules made from fully biodegradable material based on the principles of the circular economy.” However, the colleagues at Entry Engineering Member of Matador Group simply call it the “capsule machine.”
It all started with an idea, and the result is a new product—and when you think it through… delicious coffee.
The project was supported by the OP TAK – APPLICATION – Call I program.
We talked with project manager Ing. Michal Amrich about what exactly the capsule machine can do and its path to first use.
What is the result of the team’s work? What does the capsule machine do – what is its practical use, and what are its technical specifications?
I definitely can’t summarize it in one sentence. There are several outputs from the project. First, the construction design and realization of a pilot machine for roasted coffee processing—already operated by project partner Nordbeans. Also, the design and production of proprietary Nespresso capsule shapes, including the compounding of a material blend with a fully degradable polymer matrix (degradable under home composting conditions—which is important; and based on a different material than PLA, which is not suitable for home composting). The compounded mixture also includes an organic additive (a by-product of the coffee roasting process—a thin “cellulose-like” husk known as “chaff,” which roasters often have in abundance). This husk is ground and mixed into the polymer matrix at a weight proportion of about 2%. The initial form and manufacturability verification were done by Entry; the compounding was handled by project partner TUL (Technical University of Liberec). A formal output is the utility model of this material mixture, with a 50% share for us. And I must not forget the construction design and realization of the production machine for roasted coffee processing, which we are currently finalizing, aiming to launch it into series production with minimal modifications.
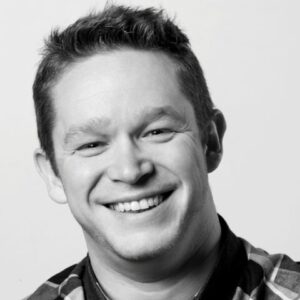
For which clients is the device intended?
The device is intended for small and medium-sized coffee roasters who want to expand their coffee product portfolios (beans, ground coffee, and other coffee-based products) with capsule coffee, which is increasingly popular worldwide. It is not about average coffee but about specialty varieties produced by top-notch roasters who insist on having full control over the entire production process—which our machine
enables. The machine is primarily built for Nespresso original-size capsules (made of aluminum or plastic); with a change of feeders and loading trays, it can also be adapted for other capsule sizes (e.g., Dolce Gusto). The process includes an integrated coffee grinder, a ground coffee buffer, a pressurized dosing unit, weighing, and manipulators for capsule and lid loading (lids processed from pre-cut shapes, but we are also developing a die-cutting solution to use material rolls).
We are also developing the construction for a die-cutting head, enabling the use of a spool with rolled material for lid production. In addition, a thermal sealing head and an inkjet printing system are integrated into the design.
Anything more about the coffee processing procedure?
The entire coffee processing workflow runs from the input hopper to the sealing of the lids under an inert atmosphere (nitrogen), preventing unwanted oxidation of the coffee and degradation of its quality. Each manufacturing step is monitored by numerous sensors (optical, capacitive, tensometric, temperature sensors, etc.). Some sensor readings are merely used to confirm that a step has been completed before the capsule moves to the next stage. Other parameters are recorded into the production log (critical for roasters), allowing precise fine-tuning for specific coffee varieties and roast degrees to ensure consistent top-quality capsule production. It’s not a shot in the dark—the quality of coffee produced on our machine is assessed by a Q-grader, a certified coffee professional (similar to a sommelier). In the Czech Republic, there are only two Q-graders, and we are lucky that one of them works at our project partner Nordbeans in Liberec.
Where does the “story” begin? Why did Entry Engineering start this project and what was the first impulse?
The story began with the vision of Pavel Paickr, who wanted to connect regional research (TUL), technological development (Entry), and product manufacturing (Nordbeans). Food processing machinery remains highly trendy, and with proper project formulation, such projects fit into EU, national, and regional strategic plans (circular economy, biodegradable materials, Industry 4.0, etc.). By maintaining good professional and friendly relationships with universities, we have access to their know-how and know how they can contribute to a joint project. This was the case here: (smiles) our boss came from TUL with plastic samples containing natural additives (buckwheat, flax, coffee grounds) and told us to come up with something. At that time, it wasn’t clear that it would turn into this specific project. Clearer contours began to take shape after visiting the Nordbeans roastery, where we
discussed the potential use of their roasting by-products. We also discussed their enthusiasm for strict production process control—hinting that any collaboration would have to involve waste being transformed into a product and the process being tightly controlled with high repeatability. The idea that it would become a capsule machine for Nespresso-size capsules crystallized even later, when we discussed contract-based capsule production at large centers—where roasters lose process control and the coffee quality starts to degrade.
How would you describe the path to the goal?
It started the classic way: project partners were identified, the project application was prepared, individual outputs and responsible parties were defined, budgets were allocated—for materials, team member salaries, and a marketing study was conducted to prove the business case was sound and not just a money burn.
Were there any milestones?
The project was divided into two annual phases:
- The first phase focused on the pilot machine and the material compound.
- The second phase focused on the production machine and the formal prototype of the fully degradable capsule.
What turned out to be the most difficult challenge to overcome?
Finding the time and space among commercial projects to focus on this R&D project.
What team was involved in preparing the project?
The preparation team was crucial for securing the grant. The project leader formulated all the technical sections and ensured that the correct information was provided for the project application. The entire project was structured and compiled by Gabriela Lencová. Technical matters on the Entry side were handled by Michal Amrich, with Roman Hruška responsible for construction, and Michal Němeček for electrical and software solutions. Material engineering from TUL (Technical University of Liberec) was provided by Jiří Bobek, Martin Seidl, and Jiří Habr. From NB (Nordbeans), Jiří Krispin contributed as a technologist and Radek Kolombo as a Q-grader. Last but not least, the Kozlov brothers, owners of the Nordbeans roastery, were involved. The same team also participates in the practical implementation of the project – sometimes it is simple, sometimes a bit more complex, but I must say that no one strayed from the original project intentions. I believe that even after the project is completed, we will still be able to look each other in the eye and discuss further collaboration.
What phase is the project currently in – and how is it doing with the first customer?
Formally, there is no first external customer yet. Nordbeans is a project partner and is currently operating the machine, testing it, and gaining practical experience by producing capsules.
They are satisfied with the machine’s operation. Feedback from the pilot phase has been incorporated into the production version of the machine. After the project ends, the commercial transfer or continuation of the machine’s operation at Nordbeans will be resolved. Another potential customer is a partner roastery in Jablonec nad Nisou. The project is now in its final phase – validation and testing of the production machine.
And very importantly: For which other clients is the machine a good fit?
The machine’s capacity is designed for fresh processing of small and medium batches of 10–25 kg, which our machine can process in about 5 hours at peak performance. Such batch sizes are typical for roasteries like Nordbeans. There are several dozen potential candidates within the Czech Republic. The commercialization plan describes in detail how to best market the project. The updated marketing study outlines not only the potential for applying our machine but also opportunities for acquisitions and future investments. After all, coffee is doing better worldwide than oil – and it smells and tastes a lot better, too.
Additional Question How many times did you dream about the project at night?
This isn’t the kind of project you dream about. On the contrary, it feels like exactly the kind of project every technician would want to work on. At first glance, it combines simple tasks like dosing, weighing, and welding – but hidden behind these are countless small details and many “buts.” You wouldn’t immediately think that coffee behaves differently based on oiliness, that it bridges in the hopper depending on grind size, or that the lids twist and need to be precisely welded onto the capsule rim. That’s why it’s extremely important for the project to be carefully planned, allowing for a fine-tuning phase where the “big boys” can play and solve problems properly.

